「CO2排出量削減」 カーボンニュートラルへ大きく貢献
通常の線形摩擦接合では、材料のβトランザス以上の温度にて接合することとなり、接合中にα⇔β変態が起こり、不安定な組織での接合となり、実際に使用するためには焼鈍処理が必要となります。
これをβトランザス以下の低温にて接合することで、無変態での接合を実現し、焼鈍処理をすることなくそのまま使用することが可能となります。
これまでの線形摩擦接合
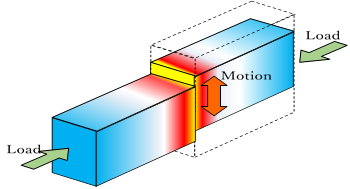
接合温度がβトランザス(変態点980℃)以上となり、接合中にα⇔β変態が生じる。
焼鈍が必要
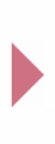
新技術!!低温摩擦接合

接合温度がβトランザス(変態点980℃)以下となり、無変態での接合を実現する。
焼鈍が不要!!
「CO2排出量削減」なぜ焼鈍が不要か!
下図は実際の接合面の組織図となります。
通常の線形摩擦接合の接合面の組織は、α⇔β変態が起こり、ラメラ状組織となっていることが見て取れます。
このような場合、接合後に熱処理を行い母材の組織に戻す必要がございます。一方、低温摩擦接合の接合面の組織は、細かい等軸粒組織となっており、これは、母材と同等もしくは同等以上の安定した組織であり、接合後の熱処理が不要となり、その分コストと納期を少なくすることが可能となります。
チタン合金(Ti-6Al-4V)での接合部 | ||
接合前母材 | これまでの線形摩擦接合 | 新技術!低温線形摩擦接合 |
![]() | ![]() | ![]() |
ラメラ(針状)組織 高温接合温度にさらされた状態 | 微細等軸粒組織 母材と同等維持用の安定した組織! |
EBSD解析 方位分布: IPF map※資料提供:大阪大学接合科学研究所
強度の証明!
チタン合金(Ti-6Al-4V)※破断時の引張強度990MPa
下図は、チタン試験片の引張試験結果となります。
通常の線形摩擦接合で焼鈍なしの場合、接合部で破断しておりますが、
低温摩擦接合の場合、焼鈍無しでもは母材で破断しており、母材と同等もしくは同等以上の強度であることが確認されております。
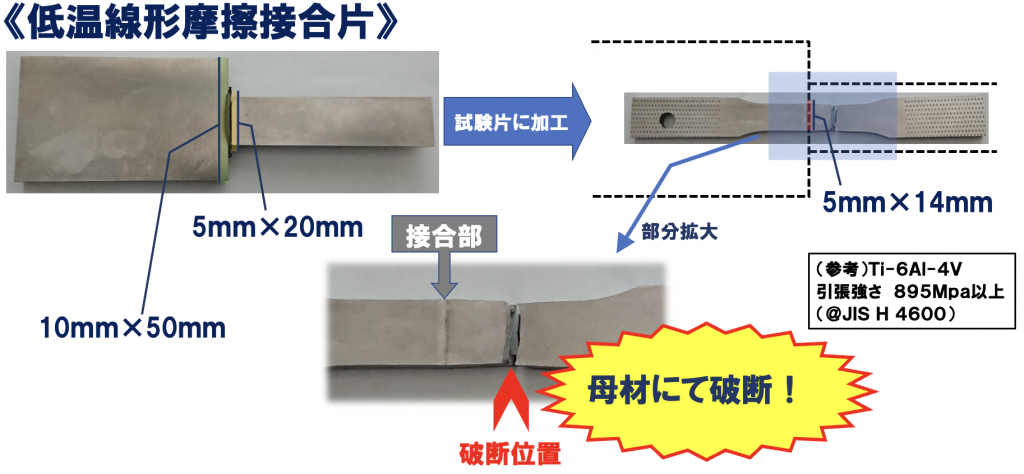
「製造コストの低下」費用比較(使用例:Tiー6AIー4V部品)
材料費においては従来削り出しを必要としていた品物も、必要箇所に必要部材を取り付けることにより、大きく材料コストを削減することが可能となります。
結果として材料費は下図のサイズだと70%、トータルコストとしては50%の コスト削減を可能とします
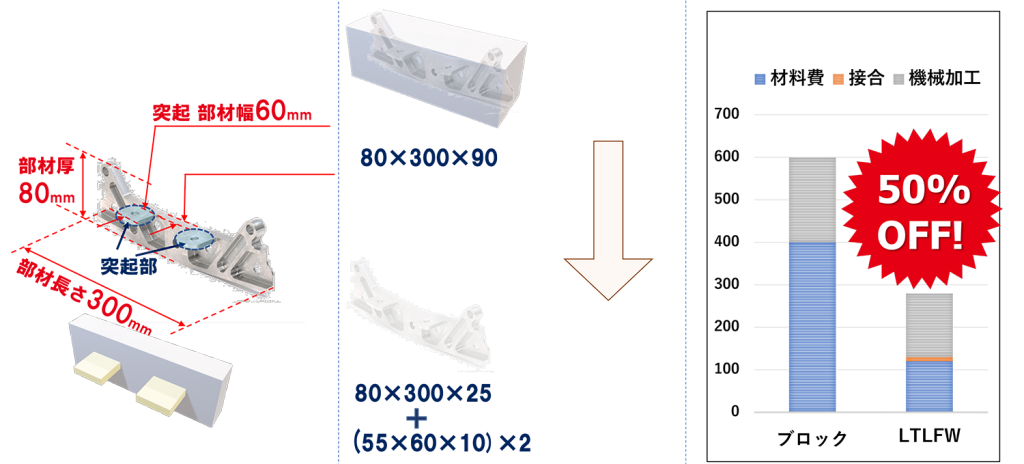
「製造コストの低下」工程時間大幅削減!
動画でご覧いただいた通り、線形摩擦接合は加工時間も大幅に削減します。
この時間の短縮と焼鈍工程が不要であることは 二酸化炭素排出量削減に大きく貢献いたします。
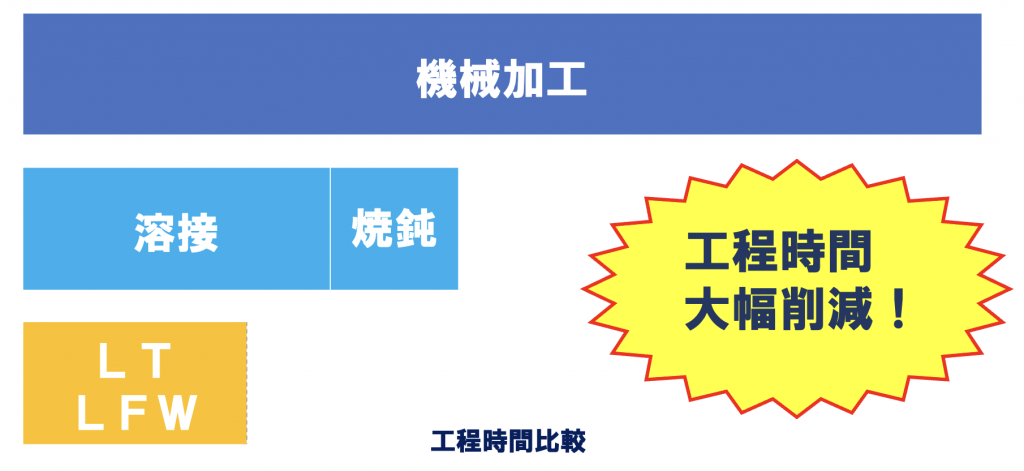
「品質の向上」安定した材料による高品質
下図は素材の安定化についてです。大きな材料の場合、内部欠陥が起こる可能性がありますが、低温摩擦接合においては安定した小さな部材の組み合わせとなり、より安定した高品質な素材を作成することができます。
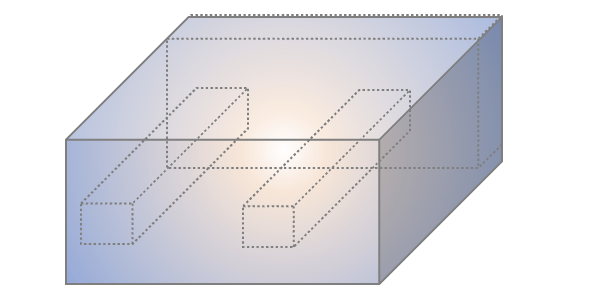
【従来品】
大きな材料の場合、内部で欠陥が発生する可能性があり、素材としても不安定な所があった。
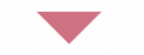
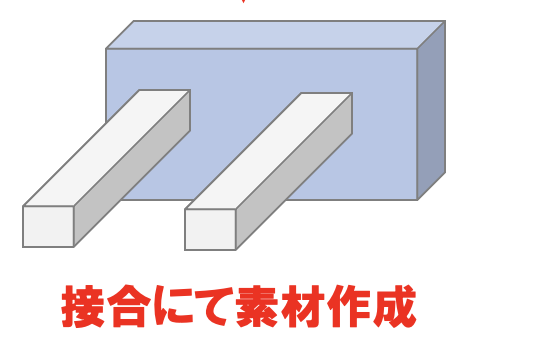
【新技術】
小さな材料の組み合わせのため、金属組織が安定して従来品よりも高品質な素材をご提供できます。
接合可能材質
下図が、低温線形摩擦接合が可能な金属の組み合わせ表となります。
異種金属の接合においても、安定した接合が可能となります。
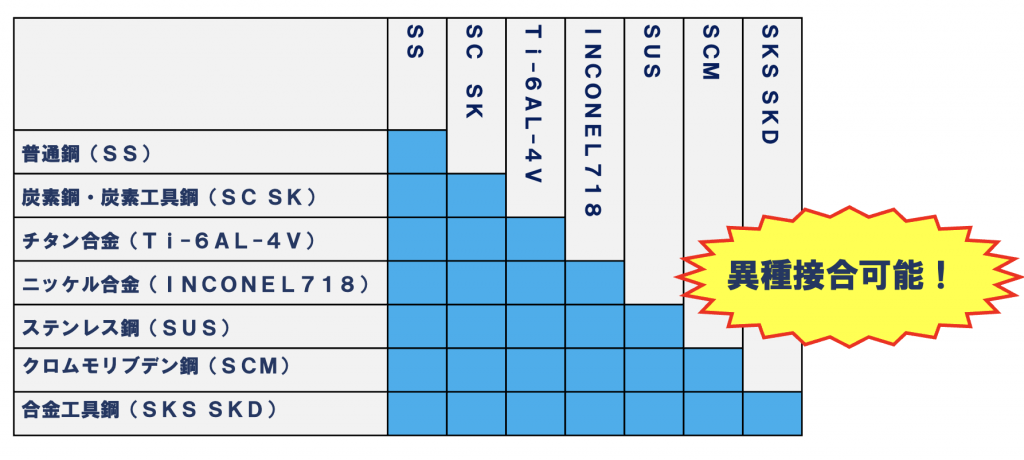
その他技術と低温摩擦接合との比較
当社の考えます低温摩擦接合の強みについてですが、「機械加工、溶接」などの従来の技術に対し、
時間・品質・必要な工具などのあらゆる点で優れていると考えております。
例えば機械加工に対しましては、短時間での製造が可能且つ切削工具等が不要な点、
また、FSWに対しましては高額なツールが不要な点で優れており大幅なコスト削減や時間短種が可能です。
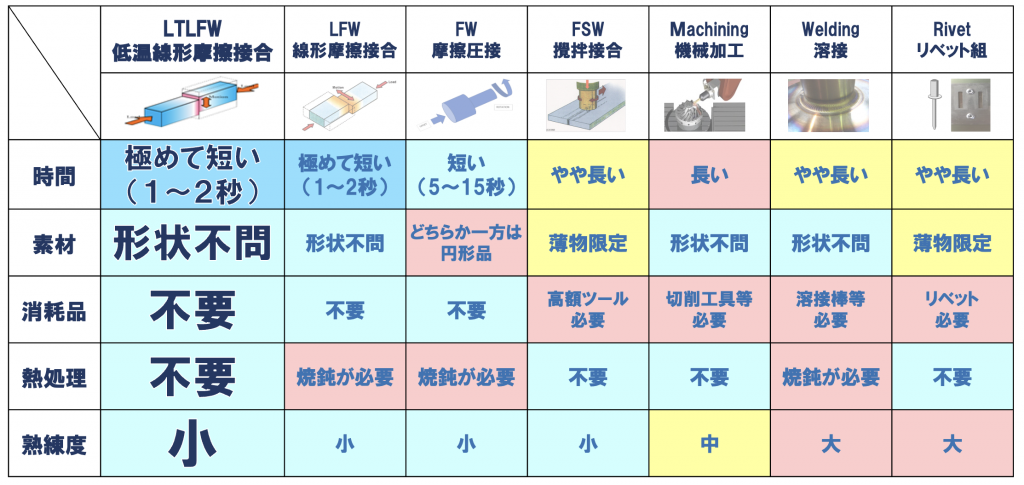